A Different Approach to the Repair of Large Industrial Structures
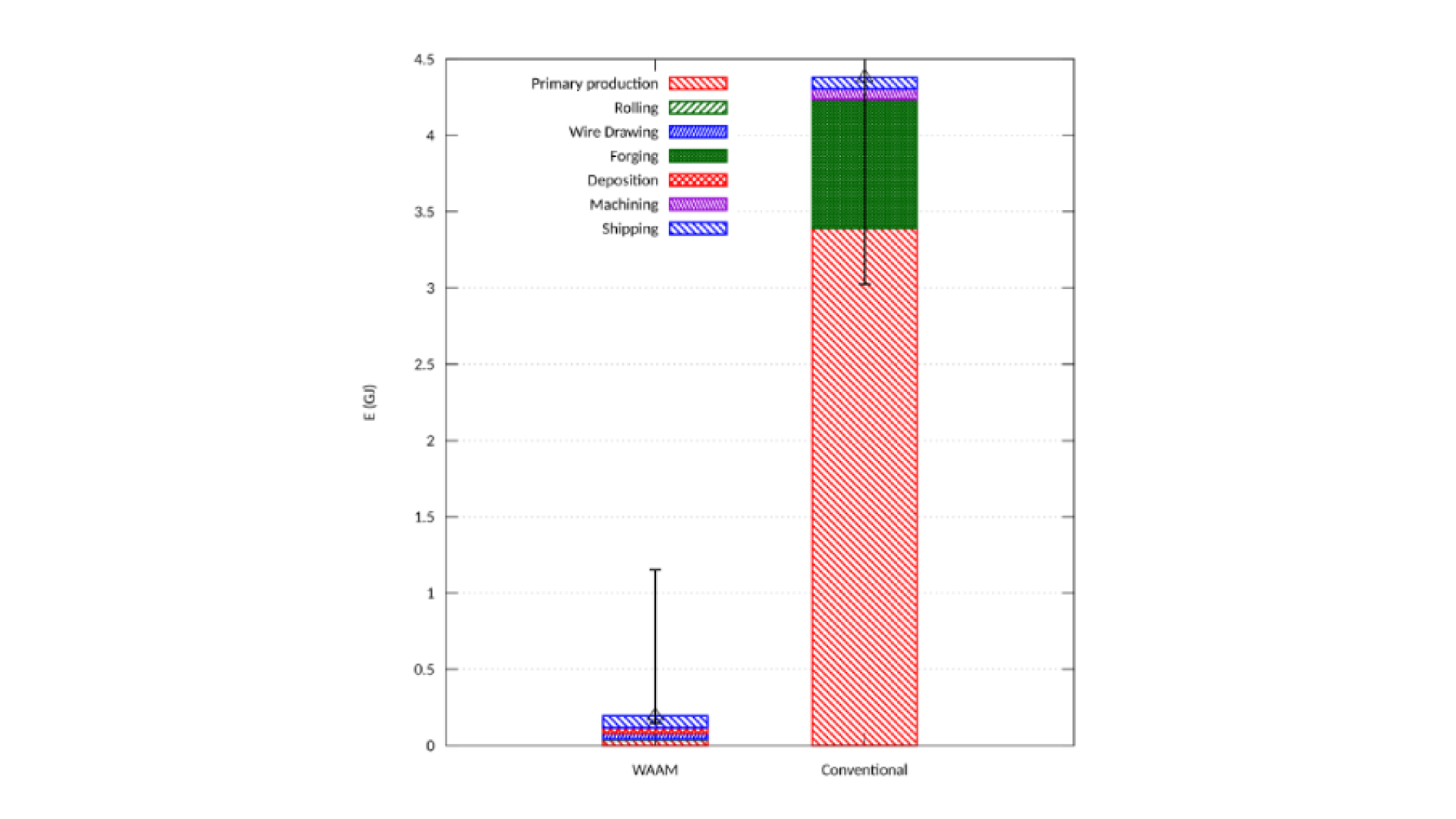
Life Cycle Assessment applied to repair by WAAM
‘Make do and mend’ might be a phrase we are more familiar with from the 1940s, however, the ethos behind it - ‘repair don’t replace’ - is gathering momentum in industrial applications. With long manufacturing lead times and supply chain reliability for replacement components becoming increasingly problematic, more operators are turning to metal additive manufacturing processes to extend the life of their large-scale components.
Life cycle sustainability assessment of repair through WAAM
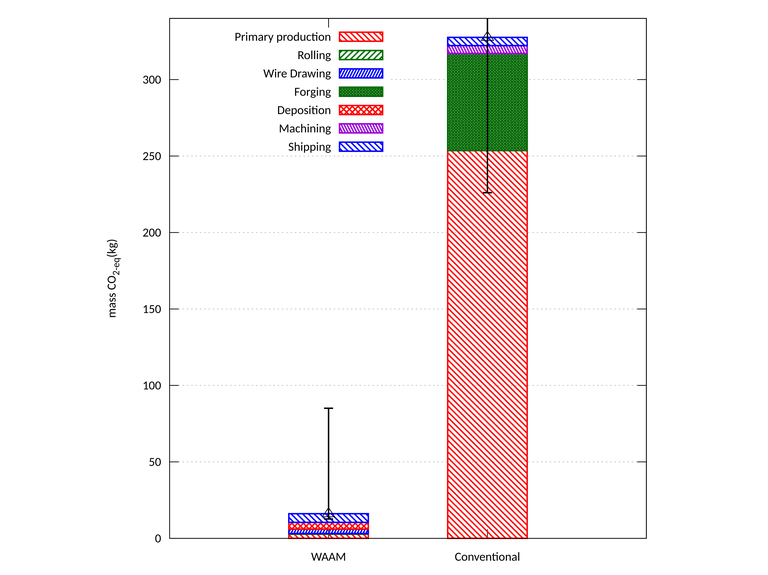
WAAM for repair of large structures
Wire arc additive manufacturing (WAAM®) is a type of directed energy deposition (DED) additive manufacturing that is used in the creation and repair of medium-to-large- components. With relatively high deposition rates, it layers metal wire using a heat source and has the potential to deliver both cost and environmental benefits compared to subtractive processes.
WAAM can be used to repair holes, cracks, segregation, inclusions, surface marks and notches. The repair is undertaken using three main steps: the removal of defects by machining, the deposition of a suitable metal material to fill the groove using WAAM and its finishing by machining.
Environmental benefits of repairing components using WAAM
According to a methodology developed to assess the life cycle environmental sustainability of repaired products using WAAM [1], this form of additive manufacturing can significantly reduce environmental impact, compared to product replacement, and be less resource intensive than other environmentally-virtuous practices like recycling.
As can be seen the potential for environmental and cost benefits can be significant when using WAAM to repair medium- to large-scale components and structures rather than replace them. More information on this life cycle assessment is available here.
Additive manufacturing and repair
When it comes to using additive manufacturing for repair, the technology delivers many benefits [2]:
- Reduced waste generation during repair process
- Reduced process time for repair
- Improved product utilisation through repair and remanufacturing
- In-situ repair and remanufacturing enabled by availability of digital designs
- In-situ and spot repair extends product life
- Component upgrade during repair process
- Product-service business models for repair and remanufacturing align business and sustainability interests
- Implementing distributed maintenance systems
- Certifying repair and remanufacturing processes
- Certifying spare parts to overcome liability issues
To find out more about extending product life through repair, why not see how WAAM can help you? For more information on how WAAM can benefit you, contact us here.