How Wire Arc Additive Manufacturing Cuts Time to Market for Marine Applications
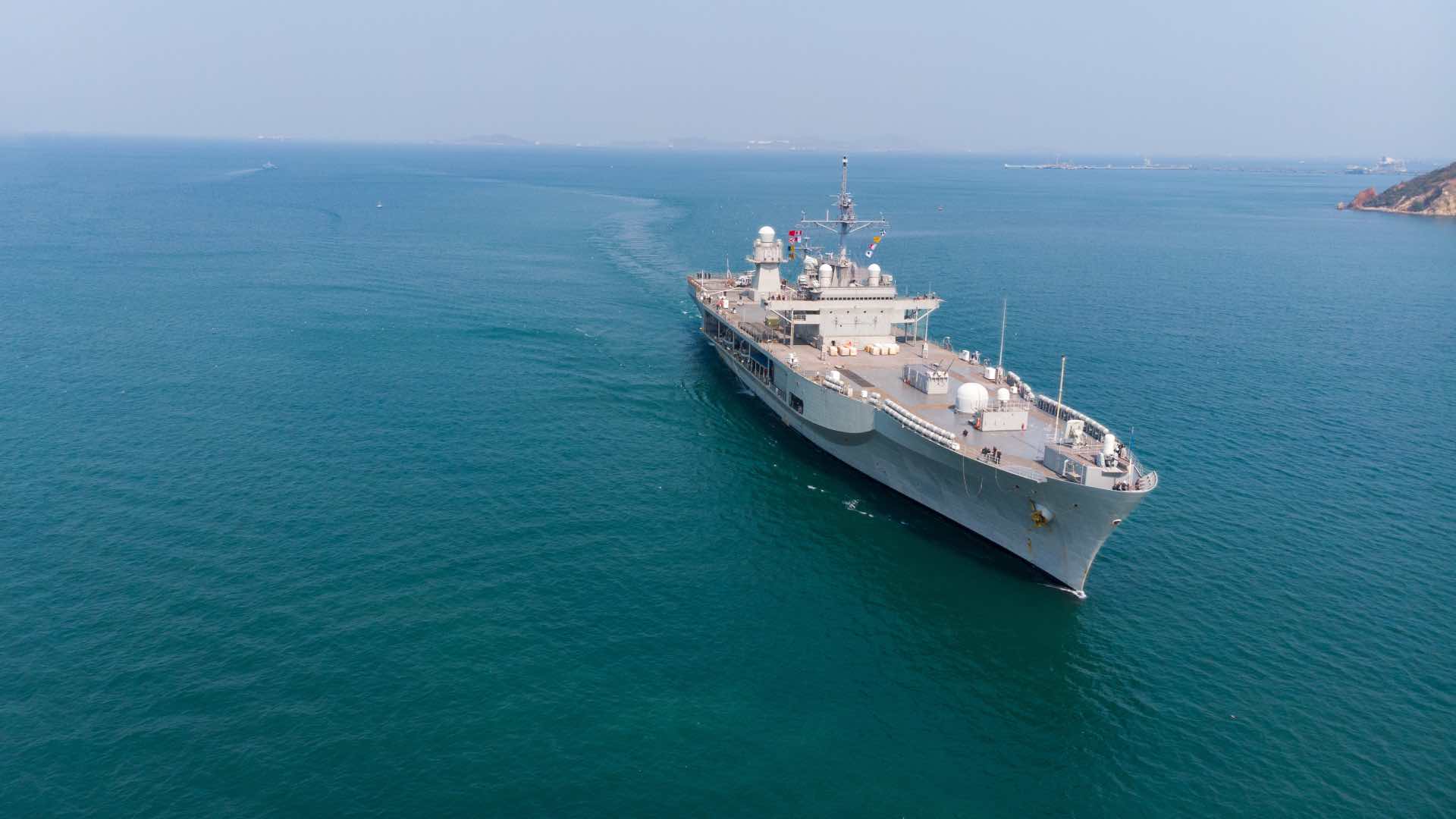
As with many other industries, the marine sector is facing increasing commercial pressures; from supply chain issues, to increased turnaround times in port. As more and more marine providers look to increase their efficiencies, one area which has significant potential for time and cost savings is the use of 3D metal component printing for both fabrication and repairs.
WAAM – cost and lead time reduction
Propellers, valves and heat exchangers are all benefiting from WAAM. This is because with WAAM it is possible to create large-scale, very near net shape preforms. Importantly, this is done without the need for complex tooling, moulds or dies and can lead to significant cost and lead time reductions for medium-to-large scale marine engineering components of medium complexity.
WAAM – component integrity
Seaworthiness is obviously paramount when it comes to a ship’s propulsion and rudder systems. As well as time and money implications, any compromise in component integrity can cause major safety issues. New and repaired components need to be robust and fit for purpose. Thanks to WAAM’s ability to fully melt the wire feedstock, which subsequently becomes part of the final structure, exceptionally high levels of mechanical integrity are created.
WAAM – supply chain and stock benefits
Just as importantly, it is far faster to produce a part using WAAM - from design to delivery – than forge or cast it. WAAM reduces typical lead times from possibly a year or more, to a few weeks or less. The nature of WAAM also means that it can enable the reduction of inventory and logistics costs by focusing on local, on-demand manufacture; helping marine operators to resolve spare part production and repair issues, quickly and as cost-effectively as possible.
Reduced material waste and component life extension
WAAM offers marine manufacturers a double blessing – the ability to cut time to market, whilst also delivering a range of environmental benefits:
- WAAM has long been used to repair structures, extending the life of components, and delivering even greater environmental and cost benefits
- The WAAM process minimises waste, and material-usage is very high at approximately 98% [1]
- WAAM-based manufacturing also delivers significant energy and CO2 emission savings.
As can be seen, WAAM offers a range of benefits to cut time to market to marine operators. For more information on how WAAM can benefit you, why not contact us here.
[1] Paolo C. Priarone, Emanuele Pagone, Filomeno Martina, Angioletta R. Catalano, Luca Settineri, Multi-criteria environmental and economic impact assessment of wirearc additive manufacturing, CIRP Annals, Volume 69, Issue 1, 2020, Pages 37-40,