Direct Energy Deposition (DED) 3D Printing: analysing cost efficiency and ROI
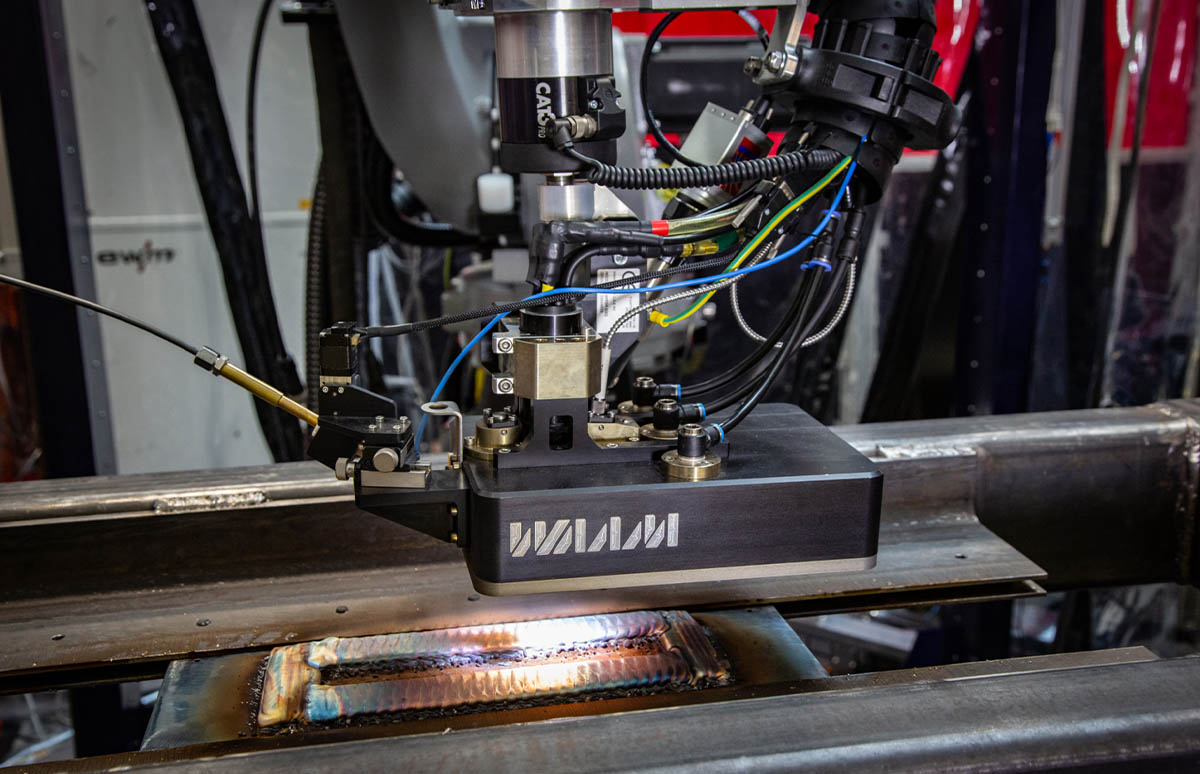
As modern manufacturing continues to develop rapidly, manufacturers need to fight for every percent of market share, and when revolutionary innovations and production volumes keep setting conditions, DED 3D printing appears to be a profitable and efficient solution. As every sector of the market is struggling hard to stay in the competition, all efforts to improve the efficiency and profitability of additive manufacturing is more than relevant.
In a rapidly changing dynamic environment of manufacturing, it is necessary to analyse the interaction of investment and return on Direct Energy Deposition technologies. Therefore, responsible mediation and qualitative analysis are required when making decisions about weighing the prospects of DED technologies in the production cycle. In fact, the issue does not concern the investment in innovative technologies, but the need for additive manufacturers to be prepared to radically change their production methods.
DED 3D printing technologies produce intricate components quickly and accurately while reducing material waste and production costs. Manufacturers must understand where and how DED will best yield benefits. The trick is to find the delicate balance between front-end investment and back-end returns making the most of production lines and profit. Often, this is done using methodologies such as Net Present Value, Internal Rate of Return, or the Payback Period.
With DED technologies, economic efficiency can be pursued into a versatile tool that challenges conventional manufacturing. As a result, additive manufacturers can quickly develop new inventions to the market. By using DED 3D printing technologies, production and procedures can be streamlined for maximum benefits and profitability.
At its heart, DED 3D printing is for manufacturers seeking to streamline their manufacturing processes while speeding up time to market. Direct Energy Deposition technologies achieve this by appropriating additive manufacturing principles to make the entire production process more efficient and flexible, thereby reducing material waste.
Most importantly, in evaluating DED's economic impact, its ability to generate concrete returns on investment is a key factor. Taking a close look at whether new technologies will pay off through thorough scrutiny of production costs, material usage efficiencies, and other factors is one of the increasingly significant issues facing organisations.
WAAM's role in DED 3D Printing technologies
WAAM’s deposition rates are higher than laser processes and the end product’s structural integrity is better when wire is used compared to powders. Using WAAM 3D printing technology, additive manufacturers can create complex geometries with speed and precision via wire-based deposition processes which means that material is not wasted, and expensive tooling costs are drastically reduced. it is one of the most cost effective and profitable DED 3D printing technology.
When it comes to Return on Investment (ROI), WAAM outperforms all other DED technologies. Its scalability and cost-effectiveness offer manufacturers an ability to respond quickly to ever demanding market of additive manufacturing. Whether WAAM 3D printing is used in the aerospace, automotive, or maritime industries, there are huge cost savings and potential revenue growth opportunities associated with it.
Our expertise in WAAM
WAAM technology enables sustainable development, creative innovation, and great return on investment in today’s rapidly changing additive manufacturing environment. It can be effectively integrated into your manufacturing workflows by analysing production expenses, material utilisation and operational efficiency. At WAAM3D, we work with our clients to help them to understand the potential of WAAM 3D Printing and how they can utilise this latest technology. We have developed state-of-the-art WAAM additive manufacturing technologies that help our customers create outstanding AM solutions for large-scale industrial metal components.
Our services include consulting, part design, business case analysis, and lifecycle drafting. Our team of WAAM specialists will print demonstrator parts and organise extensive preparatory training for your engineer and operator team. Our training packages educate your additive manufacturing engineers and machine operators covering the basic principles of WAAM technology, the printing process, and component manufacture.
With our expertise in corporate finance and project appraisal, we can demonstrate how WAAM can create value for your organisation and its stakeholders. Get in touch with us today!