Factors to Consider when Choosing a DED Process
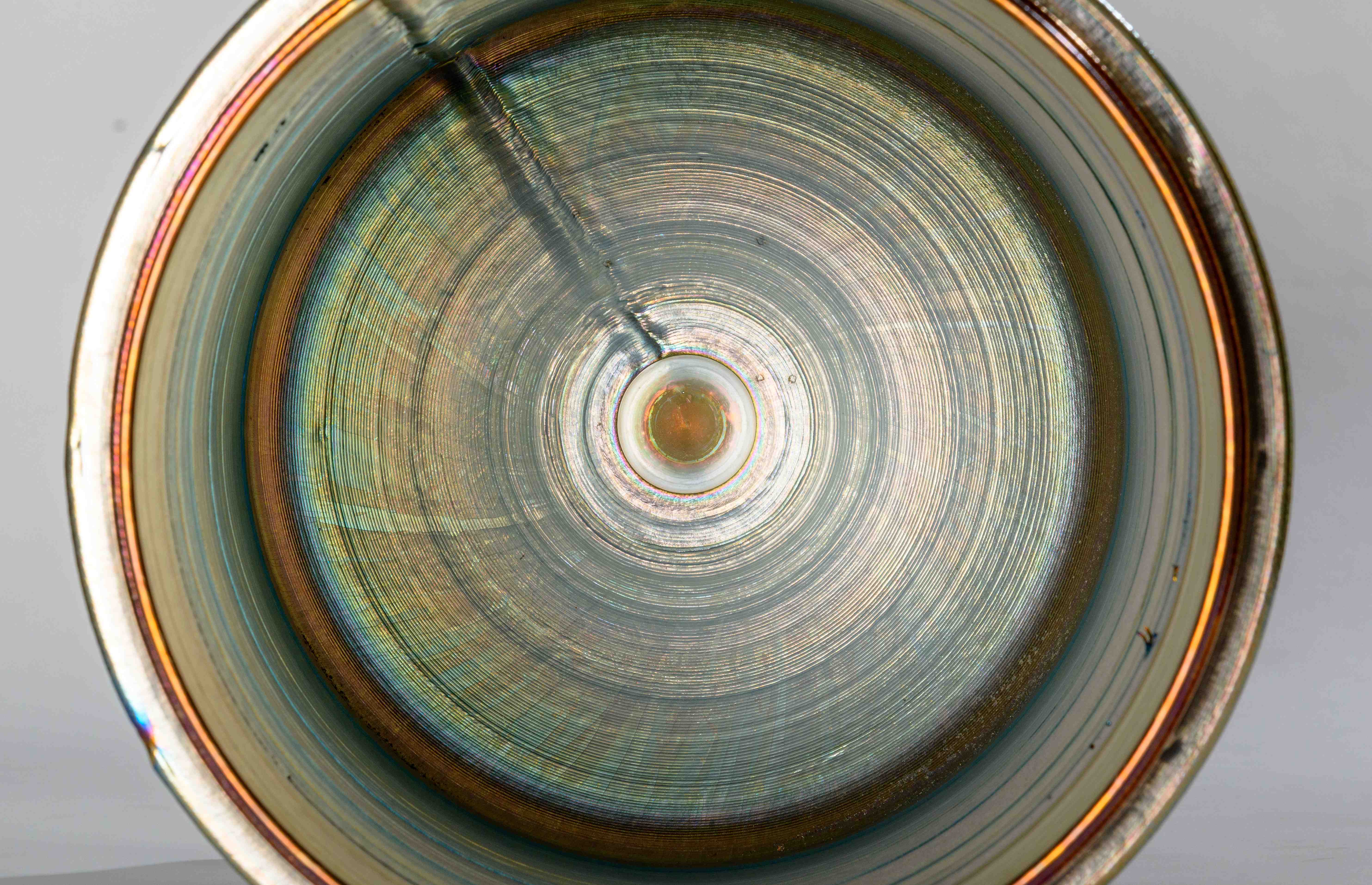
Directed energy deposition (DED) is one of the seven types of additive manufacturing technologies.
DED processes can produce exceptionally large structures, making them an ideal choice for applications that require scalability and robustness. With rapid deposition, material versatility, and large-scale production capacity, DED processes are versatile and powerful additive manufacturing tools. In addition, these processes can be used for rapid prototyping and tooling, repair and cladding and customisation projects.
Common direct energy deposition processes include:
• Laser Metal Deposition (LMD) – versatile and can be used with a variety of metal alloys.
• Wire Arc Additive Manufacturing (WAAM®) – can use a range of materials including titanium, aluminium, refractory metals, steel, bronze and copper to Invar®, Inconel® and magnesium.
• Plasma Arc Deposition – this is a subset of WAAM, which allows for the more precise deposition of the same materials mentioned above
• Blown Powder Deposition – is adaptable to various materials, including metals and ceramics.
As we explore in this blog, there are many factors to consider when choosing a DED process that is right for your needs:
Build size and volume
The size of the component will influence the choice of DED 3D printing process. Different DED systems have varying build volumes and capabilities. For example, LMD for more intricate designs and WAAM is ideal for creating large-scale metal components.
Material compatibility
The application will influence the choice of DED additive manufacturing process and material compatibility. Materials used in DED include metals - such as titanium, stainless steel, nickel alloys and aluminium, polymers and ceramics. A polymer matrix composite and metal matrix composite further enhance the versatility of DED. Furthermore, the addition of novel materials with enhanced characteristics increases the adaptability of the DED additive manufacturing process.
Layer thickness and surface finish
Each DED system has a specific achievable layer thickness and surface finish. Depending on the process layer thickness can range from several hundred microns to a few millimetres per layer. The thickness of the layer can also impact the resultant surface finish.
Precision and resolution
The required level of accuracy and detail in the deposition process will influence the choice of DED process. Factors affecting precision include control of the energy source, accuracy of the motion control system, build parameters, material characteristics, layer thickness and system calibration.
Deposition rate
The DED printing processes’ deposition rate can affect productivity. Higher deposition rates can help increase productivity, benefiting large-scale production and rapid prototyping. Factors influencing deposition rate include scanning speed, feedstock delivery rate, layer thickness, energy source power, material properties and system configuration.
Material feed
Material feed choice is influenced by the application, capabilities of the DED system, deposition rates, desired properties of the final part, feedstock availability and cost considerations. Continued additive manufacturing R&D is also expanding the range of novel feedstock materials used in DED processes.
Multiple materials
Some DED processes allow for the use of multiple materials in a single build, enabling the creation of hybrid structures. Simultaneous deposition, powder blending, sequential deposition, dual-feed systems and functionally graded materials all allow for specific characteristics to be achieved, depending on the application’s requirements.
Post-processing
Additional machining and milling, surface finishing and polishing or heat treating may be needed to meet specific quality standards or tolerances, depending on the DED process used.
Monitoring and control
Some DED processes have more sophisticated levels of process monitoring and control than others. Real-time monitoring allows for enhanced precision and quality control, promoting part consistency.
System integration
How the DED system will integrate with other technologies and processes will impact manufacturing production workflow and overall efficiency. Successful DED system integration is key to overall manufacturing efficiency.
Return on investment
It is worth considering the ROI of the DED process. Initial equipment and material costs and operational expenses can make one process more suitable over another.
Certification and standards
The DED process chosen needs to meet industry certifications and standards, especially in critical applications such as aerospace, defence, marine or medical.
It has become increasingly important to identify the most suitable DED 3D printing process in the dynamic landscape of evolving additive manufacturing technologies.
Feel free to contact us if you would like to explore the capabilities of one such DED 3D printing method, Wire Arc Additive Manufacturing (WAAM). Find out how WAAM can be used effectively for your specific application.