Directed Energy Deposition – Back to Basics
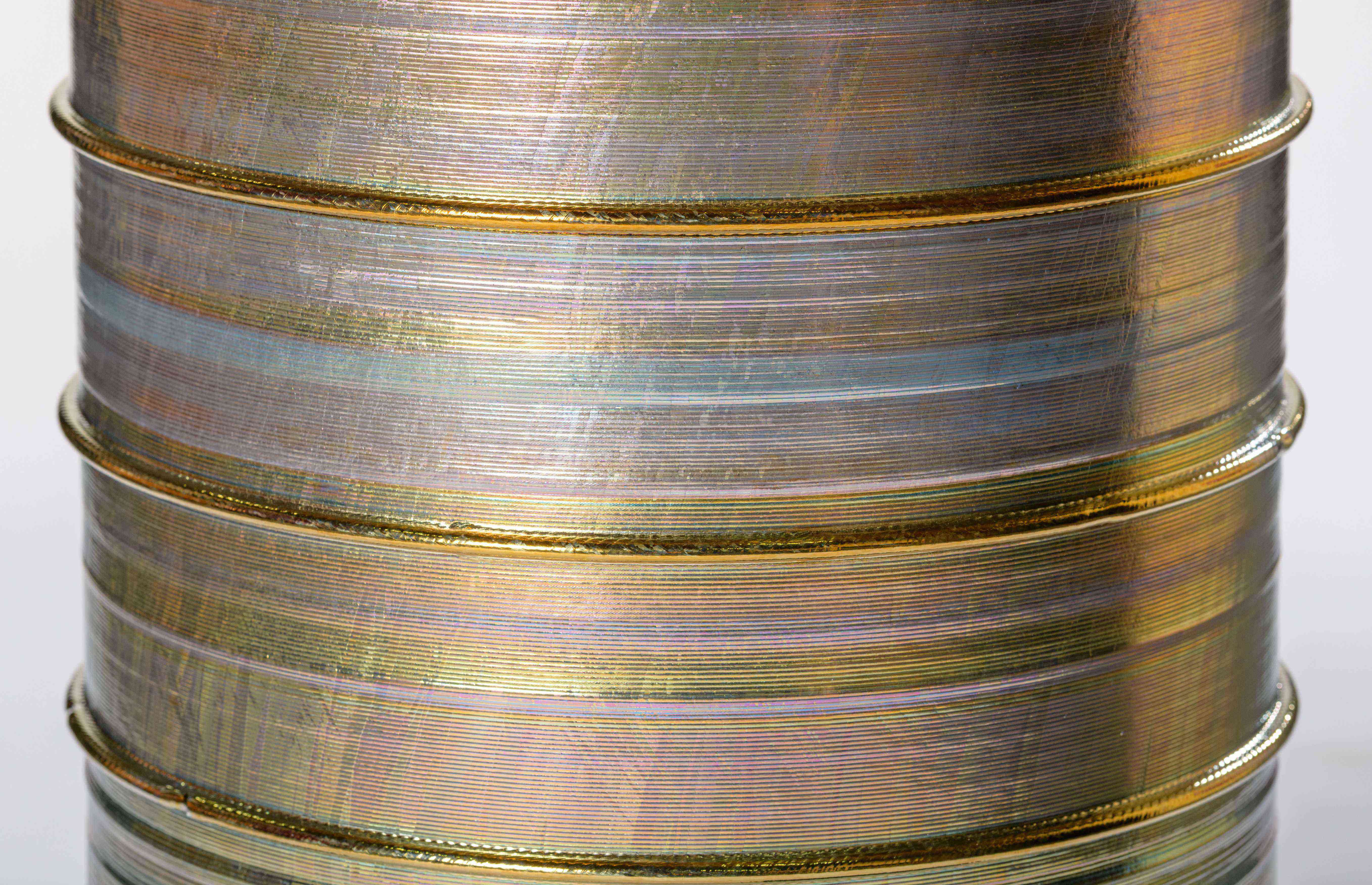
Directed Energy Deposition (DED), also known as Direct Energy Deposition, DED Additive Manufacturing, DED 3D printing and DED printing to name but a few, is a manufacturing process that is opening exciting opportunities for metal component creation and repair. Here at WAAM3D, as experts in the process of wire arc additive manufacturing - a type of wire DED - it is easy to jump ahead and go into the minutiae of deposition rates and quality control Etc.
Instead, let’s take a moment to go back to basics. Here is an overview of what Directed Energy Deposition Additive Manufacturing is and where wire arc additive manufacturing (WAAM) fits into the picture.
Directed Energy Deposition 3D printing
DED is a process that involves the melting or sintering of a material (typically in powder or wire form, using a heat source such as a laser or electron beam) to build up or repair a part layer by layer. Once the material is deposited it cools and each layer fuses with the one below, creating a stable and strong final structure.
Typical DED Processes:
· Electron Beam DED – this uses an electron beam to melt wire feedstock
· Wire Arc Additive Manufacturing (WAAM®) – this uses an electric arc to melt a wire feedstock as it is deposited onto the part.
· Laser Metal Deposition (LMD) – this is where a laser is used to melt either powder or wire feedstock as it is deposited.
DED benefits and challenges
· The DED process is used to create prototypes for product development as well as specialised parts. In addition, it can be used to repair or enhance existing components.
· Depending on the DED process chosen it is possible to create complex and intricate shapes that can be challenging to develop with traditional manufacturing methods.
· Due to the creation of the structure layer by layer, some post-deposition machining may be needed to achieve the required surface quality and dimensional accuracy.
· Commonly used materials include various metal alloys, such as stainless steel, titanium, and aluminium.
· DED delivers significant reductions in material waste compared to traditional CNC machining or forging component methods, promoting sustainable manufacturing practices and maximising cost savings (and these can be significant when using expensive materials such as titanium).
WAAM Benefits
WAAM is a cost-effective method of DED that delivers high quality components with material utilisation close to 100%. It enables the creation of very large part size and more complex design features such as internal cavities, can be incorporated.
Thanks to WAAM3D’s in depth research with Cranfield University, and their combined involvement in the UK Research Consortium ‘HPWAAM’ (High Productivity Wire Arc Additive Manufacturing group), the WAAM process has exceeded other DED techniques in terms of understanding, potential deliverables and production and cost efficiencies.
WAAM3D can now offer manufacturers:
· Increased component complexity and deposition rates - the HPWAAM group has increased steel deposition rates to 15 kg/h from a baseline of 3kg/h.
· Improved cost savings - putting down a kilogram of printed material using WAAM is cheaper than using laser - or electron-beam-based machines.
· Advanced monitoring and evaluation to deliver high levels of process control and demonstrate compliance to certification boards and regulatory bodies.
There is no doubt that DED has a wide range of benefits to offer when it comes to component creation or repair. Now, thanks to the advances being made in WAAM by WAAM3D, even more of these benefits are being commercialised by manufacturers across the globe.
If you have a project that our Team can help with, get in touch.