Expanding Horizons: Materials for DED Additive Manufacturing and Its Applications
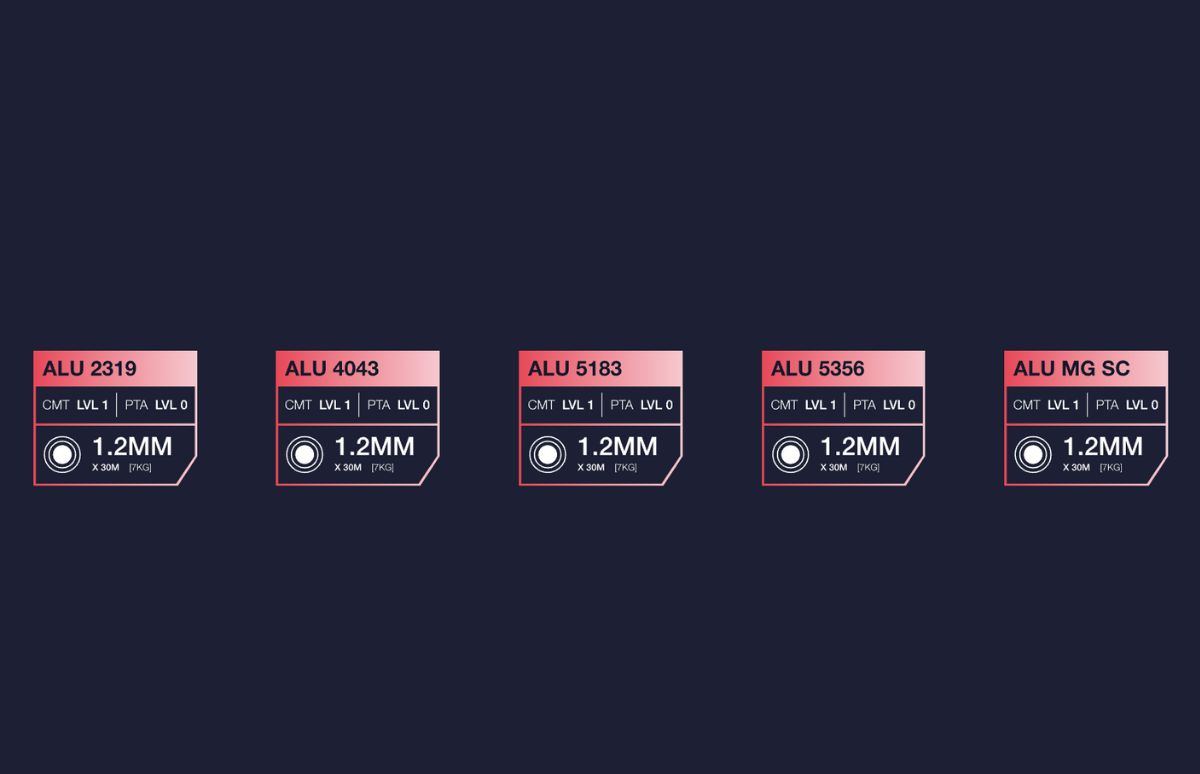
While Direct Energy Deposition (DED) is typically associated with metals, either in powder or wire form, it can also be used to deposit ceramics.
When it comes to metals, DED opens a wide array of possibilities. This method can be used to 3D print virtually any weldable metal. These include titanium and its alloys, Nickel, tantalum, tungsten, niobium, stainless steel, and aluminium. The diameter of the wire used is typically 1-3 mm, while the particle size is typically between 50 and 150 microns. DED's versatility in material selection underlines its wide applicability and potential in various manufacturing scenarios.
A broad range of materials used in Direct Energy Deposition (DED) additive manufacturing provide versatility across diverse industries. The use of metal alloys, including stainless steel, titanium alloys, aluminium alloys, nickel alloys like Inconel, and cobalt-chromium alloys, is widespread, from aerospace components to medical implants. Their mechanical properties and corrosion resistance make them ideal for use in these applications. In addition, tool steel plays a crucial role in industries requiring durability against wear and harsh conditions.
There are a wide variety of metals in this spectrum, including tungsten, which has a high melting point, making it indispensable in applications requiring high temperatures. The unique properties of ceramic materials like zirconia, alumina, and silicon nitride make them integral to specialised industries. The emergence of composite materials also signals a significant shift, providing improved mechanical properties by incorporating ceramic particles or fibres within metal or ceramic matrices. In addition to enhancing structural integrity, this fusion of materials advances additive manufacturing by expanding its application scope.
Here is a breakdown of the materials commonly used in Direct Energy Deposition (DED) additive manufacturing processes and their applications:
1. Stainless steel:
Applications: As a result of its corrosion resistance, strength, and durability, it is used in aerospace components, automotive parts, medical implants, tooling, and machinery components.
2. Titanium alloys:
Applications: High strength-to-weight ratio, corrosion resistance, and biocompatibility make these materials ideal for aerospace and defence components and medical implants.
3. Aluminium alloys:
Applications: Their lightweight properties, high thermal conductivity, and corrosion resistance make them suitable for aerospace structures, automotive parts, consumer goods and heat exchangers.
4. Nickel Alloys (e.g., Inconel):
Applications: Their excellent strength, corrosion resistance, and heat resistance make them ideal for aerospace components, gas turbine engine parts, chemical processing equipment and high-temperature applications.
5. Refractory Metals (e.g., Tungsten, Molybdenum):
Applications: Due to their high melting points and heat resistance, aerospace components, electrical contacts, and high-temperature furnace parts can be made as well as radiation shielding.
6. Cobalt-Chromium Alloys:
Applications: High strength, wear resistance and biocompatibility make them ideal for dental implants, orthopaedic implants, aerospace components, and turbine engine parts.
7. Tool Steel:
Applications: The hardness, toughness, and heat resistance of these materials makes them ideal for tool and die components, moulds, cutting tools, and wear-resistant parts.
8. Tungsten:
Applications: Due to its high melting point and density, it is used in aerospace components, electrical contacts, radiation shielding and high-temperature applications.
9. Ceramic Materials (e.g., Zirconia, Alumina, Silicon Nitride):
Applications: High hardness, corrosion resistance, and thermal stability make them ideal for aerospace components, medical implants, cutting tools and wear-resistant parts.
10. Metal Matrix Composites (MMCs):
Applications: It is often used for aerospace structures, automotive parts, and high-performance machinery components that need to be both lightweight and strong.
11. Inter-metallic (e.g., Titanium Aluminides, Nickel Aluminides):
Applications: High-temperature strength and corrosion resistance are required in aerospace components, turbine engine parts and automotive exhaust systems.
12. Precious Metals (e.g., Gold, Silver, Platinum):
Applications: Components requiring high value or specific material properties, such as jewellery, luxury goods, electronics, and dental components.
WAAM3D’s own premium wires
The thermal cycles involved in WAAM have led to WAAM3D creating new chemistries and wire making processes to achieve better wires in terms of geometrical stability and surface characteristics. As a result, the company has developed a range of approved materials that meet superior standards, such as premium aluminium wire and rods(2319, 4043, 5183, 5356 and Magnesium Scandium). Thanks to the addition of scandium and other niche elements, these signature aluminium-based alloys deliver high performance during the WAAM process.
At WAAM3D, we understand process parameters and have the knowledge to generate single or multi-material parts that meet specific manufacturer requirements. Our meticulously crafted chemistries guarantee top-notch deposition quality using superior feedstock. Visit our materials page for more information.
With WAAM3D, you get exclusive software, hardware, AM techniques, and materials. You can count on us to fulfil your requirements with unparalleled results. Get in touch with us.