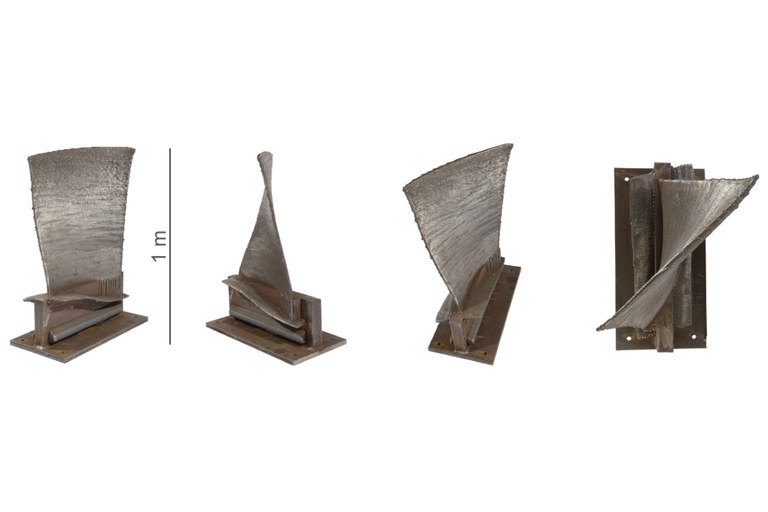
From robot- and drop-forging to horizontal-counterblow forging all owe their existence to the original art of hand forging, that dates back to at least 4000 BC. With an industrial economy built on forging, the process is tried and tested. However, thanks to recent developments, forging isn’t always the best option when it comes to component production, particularly when talking about large format structures, or the repair of existing forged parts.
A relatively recent addition to the component production toolkit is the Wire Arc Additive Manufacturing (WAAM®) technology. With the development of this technology has come new opportunities for large format 3D printing. This is particularly exciting for companies in sectors as diverse as aerospace, marine, energy, and construction, where the choice of manufacturing techniques for large parts is generally restricted to forging, casting, CNC machining, or fabrication; each of which has inherent problems.
The benefits of WAAM over forging
The main advantages are:
Quick production times - The WAAM process allows a wide variety of metal feedstocks to be used and the deposition rates of the feedstock are relatively fast. For example, between 1kg/hr and 4kg/hr for aluminium and steel, making it possible to manufacture large structures within 12 to 24 hours. Compare this to the lengthy lead-times for forged parts, typically in excess of 12 months, with further delays incurred for rough and finish machining, and the benefits of opting for WAAM for creating larger parts become evident.
High strength - forged components offer high strength, however WAAM also creates structures with exceptionally high levels of mechanical integrity that have a high yield strength, with tensile strength and elongation values that can be even better than those of comparable forged parts, especially thanks to WAAM3D’s patented in-process addition of cold-work.
Increased availability – the past year has highlighted the unpredictability of the supply chain. With limited availability of forging capabilities, the supply chain it is sensitive to disruption and, even more so in the case of machining, as access to specialised skills is required to work with materials such as titanium. However, the WAAM process offers several availability and reliability advantages for engineers looking for new and innovative ways of manufacturing large parts and complete structures reliably and in short timescales.
Realising these WAAM advantages depends on the use of the latest and most advanced production systems, such as those manufactured by WAAM3D:
- Cost-effective method of producing large and complex parts and structures
- Fast production process, from initial programming to finished part
- Near-net final part production, requiring minimal finishing
- Excellent isotropic mechanical and microstructural properties in finished parts, especially if in-process cold-work is used
- Zero deformation of finished parts, even over extended surfaces
- Multi-material structures can easily be produced
- Proven technology, using the current generation of arc sources and automation systems
- Simple to setup and program using specially developed software
- Continuous monitoring by 20 sensors and real-time control of process parameters to produce the correct part geometry
- End-effectors with local shielding eliminate the need for largescale protective enclosures
- Active cooling for increased cycle speeds
- Combination of WAAM material deposited onto forged feedstocks to leverage on the benefits of both processes delivering higher manufacturing efficiency
When compared with traditional forging processes, WAAM offers a major reduction in lead times, from over a year to a few weeks or even days, plus the ability to easily design complex shapes, with a significant reduction in unit cost.
For more information, contact us here.