WAAM – Answering Frequently Asked Questions (FAQs)
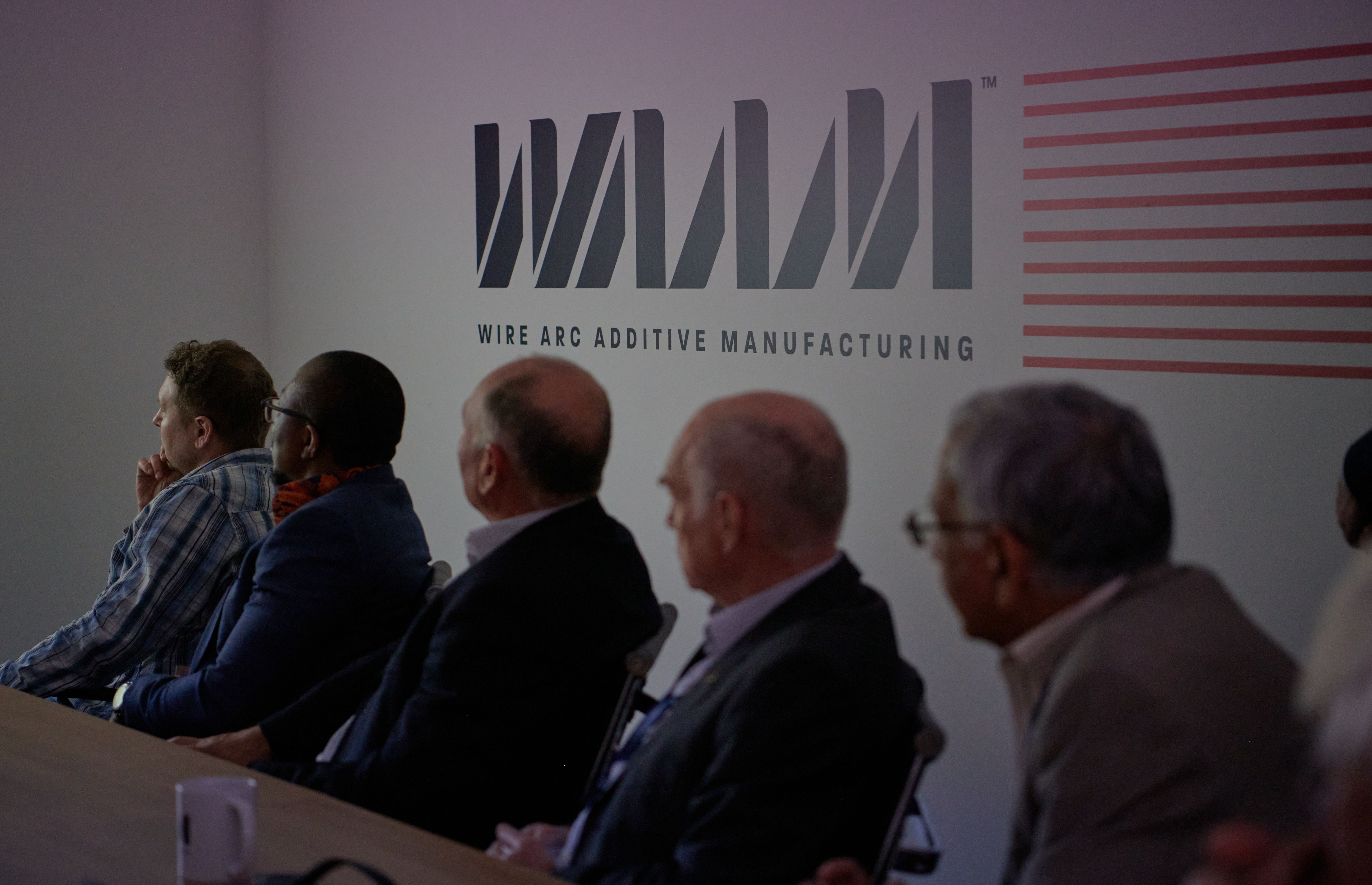
Wire Arc Additive Manufacturing, or WAAM for short, is an exciting large-scale 3D printing technology that has the potential to significantly change component design and delivery. As a relatively new technology, here are some of the most common WAAM questions answered:
What is Wire Arc Additive Manufacturing?
In essence, WAAM is the process of building a 3D structure using an electric arc to melt wire feedstock onto a metal base plate. The wire is melted in a sequence of bead strings which are built up layer on layer, as the robotic head automatically moves the printing head backwards and forwards in a pre-programmed pattern. It is part of the DED family of additive manufacturing processes and WAAM is ideal for both the production of original structures and to repair metal parts. Click here to see how it is different from more conventional methods such as forging.
What are the advantages of WAAM?
- Waste reduction and cost reduction – WAAM minimises expensive material waste (For aerospace WAAM’s buy-to-fly ratioi (BTF) is <2). It is a cost-effective Additive Manufacturing approach for component fabricationii and can deliver cost savings of up to 70% compared to machining from solid.
- Lead time reduction - WAAM replaces long lead-time processes, such as forging and casting. It can cut the time for a large forging from over a year to a matter of weeks for the entire process.
- Large size components – WAAM exploits the power of MIG and plasma welding technologies to create medium-to-large scale metal structures. To date, the largest sized WAAM3D component is 6m x 1m, built in one go!
- Freedom to choose from a wide range of materials – WAAM can create structures in a range of materials (amongst these are titanium, aluminium, refractory metals, steel, bronze and copper to Invar®, Inconel® and magnesium). You can find some mechanical properties here
- Design flexibility - the flexibility of WAAM’s process means that component design can be altered at short notice, allowing for adaptations to be accommodated with minimum difficulty.
- Stand-alone or integrated solution - WAAM can be used to build each part from the ground up, or integrated alongside other techniques such as forging, casting or CNC machining. It can also be used for the customisation and repair of existing components.
How can I find out if WAAM is for me?
If there is a demand within your organisation for the creation of new medium-to-large scale metal components, or the customisation and repair of existing ones, then WAAM could deliver you significant cost, time and material savings. Click here to find out the five questions you should ask when thinking about WAAM, or discover more about the WAAM journey over the years, and the benefits of WAAM when looking to repair components.
Where can WAAM process be used?
Aerospace - simplify manufacturing operations and reduce the cost of integration for structures used in the commercial, defence or space sectors.
Energy – improve supply chain management, deliver on sustainability targets and reduce the lead time on projects with WAAM.
R&D - develop intellectual property, deliver grants, write high-impact papers, and support local industrial ecosystems by exploiting WAAM3D’s open-architecture hardware-software platforms.
Marine - overcome challenges with large castings, spare parts and the cost of corrosion-resistant components using the WAAM process to deliver cost savings.
Cladding and Repair – improve the wear or corrosion characteristics of components, or repair them to extend their useful life, whilst improving organisational environmental performance.
What should I look for when selecting a WAAM company/partner?
This is an evolving technology, so it is important to choose a WAAM partner that can support not only the present but future component requirements with the latest WAAM developments. It is also key to choose a provider who can support your business across the entire WAAM value chain; so, from exploration to implementation and production and with inputs, products, services, and outputs.
WAAM3D sees component production as a partnership. From Cranfield’s core competence of processes, software, and hardware, to WAAM3D’s suite of innovative products and services, WAAM3D is the only provider of a total technology solution that covers the entire WAAM value chain.
If you have a project that our Team can help with, get in touch.